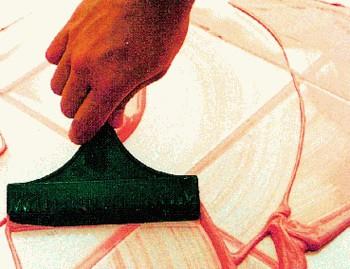
Asia has become an emerging market for dry mortar development. In Southeast Asia and East Asia, the development of dry-mix mortar products is concentrated in large cities. In these cities, the economy has grown rapidly, the population has increased rapidly, and the demand for environmental protection has become higher and higher. Mortar products were converted from dry-mixed mortar to dry-mixed mortar.
Singapore has been using dry mortar for 10 years, and it mainly relied on imports in the early days. By the year 2000, Singapore had a production capacity of 1.3 million tons, and its production capacity has increased in recent years. Singapore's dry-mix mortar is nearly saturated due to the rapid increase in production capacity. In 2003 and 2004, the dry mortar output in Singapore was 1.3 million tons, and the output in 2005 showed a downward trend.
Hong Kong dry mortar has not yet entered a large stage of development. Most of the mortars for decoration use imported materials. Some mortars for construction sites use commercial mortars, and some use imported dry mortars. The use of mortar on site has been restricted but not prohibited. So far, Hong Kong has only one upper-scale production line and is an EP company investing in Hong Kong with a design capacity of 300,000 tons per year.
The production of dry mortar in South Korea began in the mid-1990s. Before the construction, mortar was used on site. In view of the construction efficiency and quality of dry-mixed mortars that are superior to traditional on-site mixing, dry-mixed mortars have been rapidly developed in Korea. In 2002, the annual consumption of common dry mortar for floor and decoration in Korea was about 3 million tons. It is expected that dry mortar will account for 80% of the market in the coming years.
In addition, countries such as Vietnam in Southeast Asia will also accelerate the development of dry-mix mortars in the coming years. This will have an impact on the dry mortar market in China. Although experiencing the impact of the financial crisis, the demand of emerging markets such as Southeast Asia and China is still conducive to the steady development of tile adhesives.
The use of less amount of tile, good effect, low cost and high efficiency tile adhesive is the most favored special mortar in developed countries. After more than 10 years of development in China, tile adhesives have inherited the responsibilities of society and their children and grandchildren, and a large number of mortar companies are facing challenges and challenging the weaknesses of traditional craftsmanship. In 2010, the market for tile adhesives was well-developed, and it has made considerable progress. Not only in the tooling but also in the horn of home decoration for large-scale people.
The rapid development of dry mortar in Europe and the United States has the following reasons: First, increasing labor costs; Second, quality requirements, in order to compete in a saturated market, we must meet the requirements of high-quality construction; Third, mechanization The use of construction and pre-mixed mortar can increase construction efficiency and reduce the proficiency of workers; Fourth, it can save material costs and the use of materials; Fifth, to meet the requirements of some new wall and building materials for mortar, Special mortar products are required for polystyrene foam boards, aerated concrete and similar building materials. In addition, environmental issues have become more and more important. In some European countries, there are also strict restrictions on radiation and odors in building materials.
Nowadays, European and American ceramic tile sticking methods are almost all based on "thin layer technology". At present, this new sticking method is becoming more and more popular in the world. The so-called thin-layer technology, the notched trowel technique, is to apply the thickness of the adhesive trowel evenly to the entire wall of the tile to be tiled, and then use a notched trowel (a kind of wipe that has a height of 6mm every 6mm). Scratch the surface to produce a 6mm high stripe-like mortar bar on the surface of the thin layer mortar. When the tile is placed, the mortar is squeezed to form a uniform 3mm thick adhesive layer with no cavity, and the thickness is small, resulting in less material consumption. The simple technique of spacers can be used to increase the paste speed by 5 times. . This thin layer technique requires the following advanced special tile adhesive system.
Almost all tile adhesives use cement as the main adhesive. Cement and sand are usually mixed at different proportions on a construction site. The proportion of this mixture (within certain limits) is determined mainly in accordance with local construction techniques rather than technical rationality. However, this mortar mixing method will have problems when used in thin layer technology. The thin coating layer causes water to infiltrate into the substrate, resulting in faster water loss and loss due to evaporation. Therefore, additives must be incorporated into the mortar. Usually additives are added directly to the mortar in a liquid state (the so-called two-component system). This method has almost never been adopted. The reason is: the measurement accuracy is not enough; additives with relatively high additive prices may be wasted; some additives can only be purchased liquid products, and thus there is a risk of frost. Originally only mortar liquid additives were purchased. It was not until 1958 that Vinnaps redispersible polymer powders, which were developed by Weikai Chemicals Co., Ltd., were successfully used for the first time to obtain powdered additives.
At present in Europe, to meet advanced quality requirements, more than 90% of cement tile adhesives have been mixed by manufacturers (known as single-component systems, also known as dry-mix mortars). Apart from sand and cement, the most important additives are water retention agents and toughening polymers. On the one hand they promote more water retention and on the other hand the mortar layer has sufficient toughness. Dry mix mortar only needs to be mixed with the water needed to reach the desired consistency at the construction site.
Using a pre-mixed system from the manufacturer can also produce special-purpose special tile adhesives, ie composite compounds that cannot be prepared on the construction site.
Due to the use of a single-component system, only the only packaging paper bag is rubbish, which has added a positive collateral effect from the perspective of environmental protection. At present, more than 90% of tiles that have been laid in Europe and the United States use thin layer technology. Therefore, thin-layer technology also sets relevant standards. One of the most important standards is DIN 18156/1, which specifies the requirements for thin-layer tile adhesives; the other is DIN 18157/1, which specifies its use. The main indicator of tile adhesives is their cohesive strength (or shear strength according to other standards). According to the commonly used standards, the adhesive force must not be lower than 0.5 MPa after storage in standard storage, aqueous storage, high temperature storage, and freeze-thaw cycles.
From the market point of view, in the next few years, the competition in enterprises will begin to take shape. The enthusiasm and giant vision of giants for the larger market are the main theme of the future tile adhesive industry. The product will enter the era of brand competition. Tile adhesives will be more and more valued by the chasers. The quality of the products directly reflects the people's ideas and positioning. The development of the technology is to tap tiles into a vast market.
High Speed self-Recovery Rapid doors are the technological evolution of old, PVC high speed doors or heavy folding doors, now obsolete and not suited to today's industrial needs.
High-quality panels, the resistive safety edge fitted to the bottom edge of the door, photocells and barriers make this product both safe and durable, being totally self-repairing, thanks to its special [Anti Crash System".
This door designed with a perimeter structure in galvanized or stainless steel, which is ideal for sliding panels. The door panel rides effortlessly within a track, thanks to the special profile and hinge designed by us, requiring low maintenance. The panel is rolled up on a roller placed within the upper crossbeam.
The door can be equipped with a counterweight or ups batteries, to fully open the door in case of power failure, and can also be equipped with large transparent sections to create a brighter and safer working environment.
Self-Repairing Door Curtain made of reinforced PVC, with flexible weighted soft bottom edge.
The edge of curtain has continuous injection molded teeth that then move up and down in a self-lubricating polyethylene track attached to structural galvanized side frames.
Self-Recovery Rapid Door,Self Recovery PVC Rapid Door,Self Recovery Rapid Rolling Door,Self Healing Roll Door
Shenzhen Hongfa Automatic Door Co., Ltd. , https://www.selfrepairinghighspeeddoor.com