Integral hot runner
Integral hot runner technology
As hot runner technology is widely used in plastic injection molds, the traditional way of connecting the runner plate to the nozzle under pressure is gradually replaced by an integral hot runner system. In recent years, large and medium-sized injection molded parts have also adopted the threaded connection of the nozzle and the flow path plate when the needle-type multi-nozzle injection is used.
Integral hot runner
The integrated hot runner system has been around for many years. The ejector nozzle is used for a small multi-cavity small part. When the distance between the axes of the small nozzles is 10-20 mm, the nozzle is screwed to the flow channel plate, so that the hot runner system is compact.
This threaded multi-nozzle is mounted on a small volume flow channel plate. The elongated nozzle has better flexibility. There is bending deformation in the working state to compensate for the lateral thermal expansion of the flow channel plate. The nozzle relies on the flow plate to transfer heat without a heating coil. The coupling thread should have sufficient strength and high precision to be disassembled. The seal between the nozzle end face and the bottom surface of the runner plate hole holder must be reliable. Thermal compensation of large-sized runner plates is difficult to achieve. Nozzles with a diameter of 10 mm or more lack flexibility under bending deformation, and such a monolithic structure has not been used for a long time.
Demand for integrated hot runner development
In recent years, there have been many consumer electronic products such as tablet computers, game consoles, and mobile phones, and the output has been large. Nowadays, the application ratio of the needle valve nozzle is higher than that of the open nozzle. If the plastic melt is directly injected into the surface of the injection molded part at the gate of the needle valve nozzle, the gate mark protrudes on the working surface of the thin plate. The gate has a large temperature change on the thermal barrier between the hot runner nozzle and the fixed mold cavity. The plastic melt filling has a high shear rate and unstable flow, and there are often defects such as flow marks in the vicinity of the gate on the injection molded part. Nowadays, the timing sequence of the drive cylinder or cylinder of the needle valve nozzle can adjust the position of the fusion joint during the trial process. The injection point of the multi-nozzle of the integral hot runner is on the cold runner, and the position and dimensional accuracy of the injection point on the fixed template is not high, which is suitable for the application of the integral hot runner.
Http://news.chinawj.com.cn
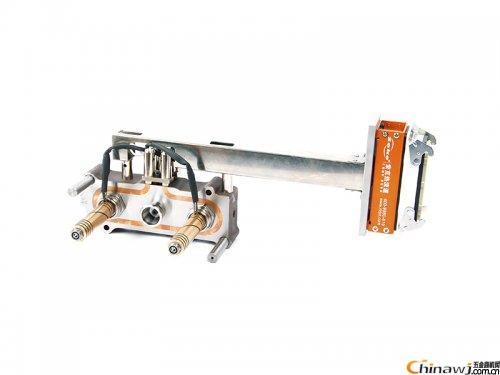
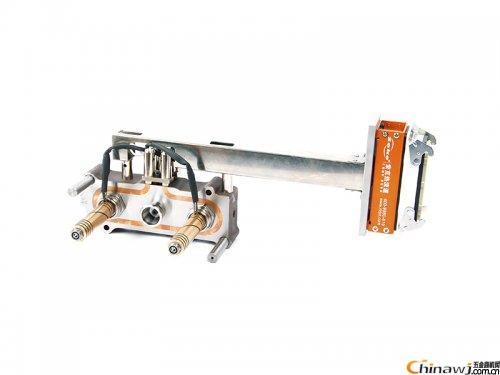
KMP Komatsu Parts,KMP Komatsu Spare Parts,KMP Komatsu Undercarriage Parts,Quality KMP Komatsu Parts
JINING SHANTE SONGZHENG CONSTRUCTION MACHINERY CO.LTD , https://www.sdkomatsuexcavatorparts.com