Last year, the turnover of automakers around the world increased, with the United States, China, India and Russia showing the largest increase. However, the rapidly increasing number of cars also poses some special challenges for production. For example, for component manufacturers, not only are they required to cope with increasing production volumes, but they must also ensure the safety of the production and the quality of the accessories. In fact, even the smallest accessories, some shapes are very complex and need to be produced with higher precision. This requirement also extends to the production industry of related specialized equipment. To meet market demands, a system solution such as EMAG's VLC 100 G inverted grinding center came into being. Grinding experts believe that it provides efficient and precise machining processes specifically for the production of small clamps.
The production of small clamps is often huge. For example, the demand for accessories such as gears, planetary gears, sprocket gears and flange components required for passenger cars is often in the millions. The production cycle of these accessories has been shortened to one day. For example, the gear internal teeth must be ground in the shortest possible time, and the loading unit of the grinding machine must be loaded into a new workpiece as quickly. In many production environments, this is a critical time period because run-off time is often a decisive factor in the economics of the production process.
Automatic loading of workpieces delivers excellent throughput with a short processing cycle. It is EMAG's VLC 100 G inverted grinding center for the processing of small clamping parts with a maximum diameter of 100 mm. The machine uses the picking system to automatically load the workpiece. When machining the workpiece, an automated system also places the next workpiece to be machined on the endless conveyor belt, which reduces machine idle time and increases production efficiency. Another advantage is its inverted machining concept, which ensures that the grinding chips fall unimpeded into the bottom and are then shipped out.
Integrated quality control measurement functions are also integrated into the machine, so quality monitoring can be performed in real time throughout the production process. The measuring probe is located between the processing area and the loading and unloading unit, where it is optimally protected against various forms of contamination.
An important feature of using two different grinding wheels, the VLC 100 G, is that it has two grinding spindles to choose from. You can use them for different grinding operations, such as roughing or fine grinding. In other words, the first grinding wheel is “roughed†to remove excess material from the original at high feed rates (for this purpose, the CBN wheel used is specifically designed to counteract the necessary impact), and Two grinding wheels (different specifications) take over the fine grinding work. Even the most complex geometries guarantee a perfect surface finish. Thanks to this combination of intelligent tools, EMAG design engineers have succeeded in significantly reducing grinding time. “The first wheel was designed for rough grinding and the second wheel for fine grinding, so especially for large-volume grinding, the two grinding wheels have a shorter machining cycle than a grinding wheel,†said Emak Salah. Dr. Guido Hegener, general manager of the machine tool company, explained.
The convincing grinding concept combines the rapid replacement of workpieces with efficient grinding processes to represent one of the most compelling new ideas, which is not surprising. It is clear that the emergence of the VLC 100 G is in line with the development of strong growth in vehicle production. The rapid increase in the production of auto parts calls for the emergence of a new concept of processing equipment that blends seamlessly with existing production. The two features of the VLC 100 G ensure this. “Programming the workpiece with the new EMAG NAVIGATOR software is simple and intuitive, saving valuable setup time. This is an inestimable advantage for many production environments,†Dr. Hegener further confirmed. In addition, the VLC 100 G has a very small footprint and a single independent machine tool of only 4.5 square meters, making it easier for production planners to work, and ensuring that new machines with such production facilities will not be added in the future. Limited by ground space.
Figure: Dressing device with diamond roller.
The production of small clamps is often huge. For example, the demand for accessories such as gears, planetary gears, sprocket gears and flange components required for passenger cars is often in the millions. The production cycle of these accessories has been shortened to one day. For example, the gear internal teeth must be ground in the shortest possible time, and the loading unit of the grinding machine must be loaded into a new workpiece as quickly. In many production environments, this is a critical time period because run-off time is often a decisive factor in the economics of the production process.
Automatic loading of workpieces delivers excellent throughput with a short processing cycle. It is EMAG's VLC 100 G inverted grinding center for the processing of small clamping parts with a maximum diameter of 100 mm. The machine uses the picking system to automatically load the workpiece. When machining the workpiece, an automated system also places the next workpiece to be machined on the endless conveyor belt, which reduces machine idle time and increases production efficiency. Another advantage is its inverted machining concept, which ensures that the grinding chips fall unimpeded into the bottom and are then shipped out.
Integrated quality control measurement functions are also integrated into the machine, so quality monitoring can be performed in real time throughout the production process. The measuring probe is located between the processing area and the loading and unloading unit, where it is optimally protected against various forms of contamination.
An important feature of using two different grinding wheels, the VLC 100 G, is that it has two grinding spindles to choose from. You can use them for different grinding operations, such as roughing or fine grinding. In other words, the first grinding wheel is “roughed†to remove excess material from the original at high feed rates (for this purpose, the CBN wheel used is specifically designed to counteract the necessary impact), and Two grinding wheels (different specifications) take over the fine grinding work. Even the most complex geometries guarantee a perfect surface finish. Thanks to this combination of intelligent tools, EMAG design engineers have succeeded in significantly reducing grinding time. “The first wheel was designed for rough grinding and the second wheel for fine grinding, so especially for large-volume grinding, the two grinding wheels have a shorter machining cycle than a grinding wheel,†said Emak Salah. Dr. Guido Hegener, general manager of the machine tool company, explained.
The convincing grinding concept combines the rapid replacement of workpieces with efficient grinding processes to represent one of the most compelling new ideas, which is not surprising. It is clear that the emergence of the VLC 100 G is in line with the development of strong growth in vehicle production. The rapid increase in the production of auto parts calls for the emergence of a new concept of processing equipment that blends seamlessly with existing production. The two features of the VLC 100 G ensure this. “Programming the workpiece with the new EMAG NAVIGATOR software is simple and intuitive, saving valuable setup time. This is an inestimable advantage for many production environments,†Dr. Hegener further confirmed. In addition, the VLC 100 G has a very small footprint and a single independent machine tool of only 4.5 square meters, making it easier for production planners to work, and ensuring that new machines with such production facilities will not be added in the future. Limited by ground space.
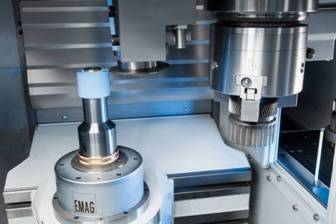
GUOLONG PRECISION VALVE CO.,LTD , https://www.glstovevalve.com